Turning concept into reality: Approaching a major Milestone!
January 3, 2024
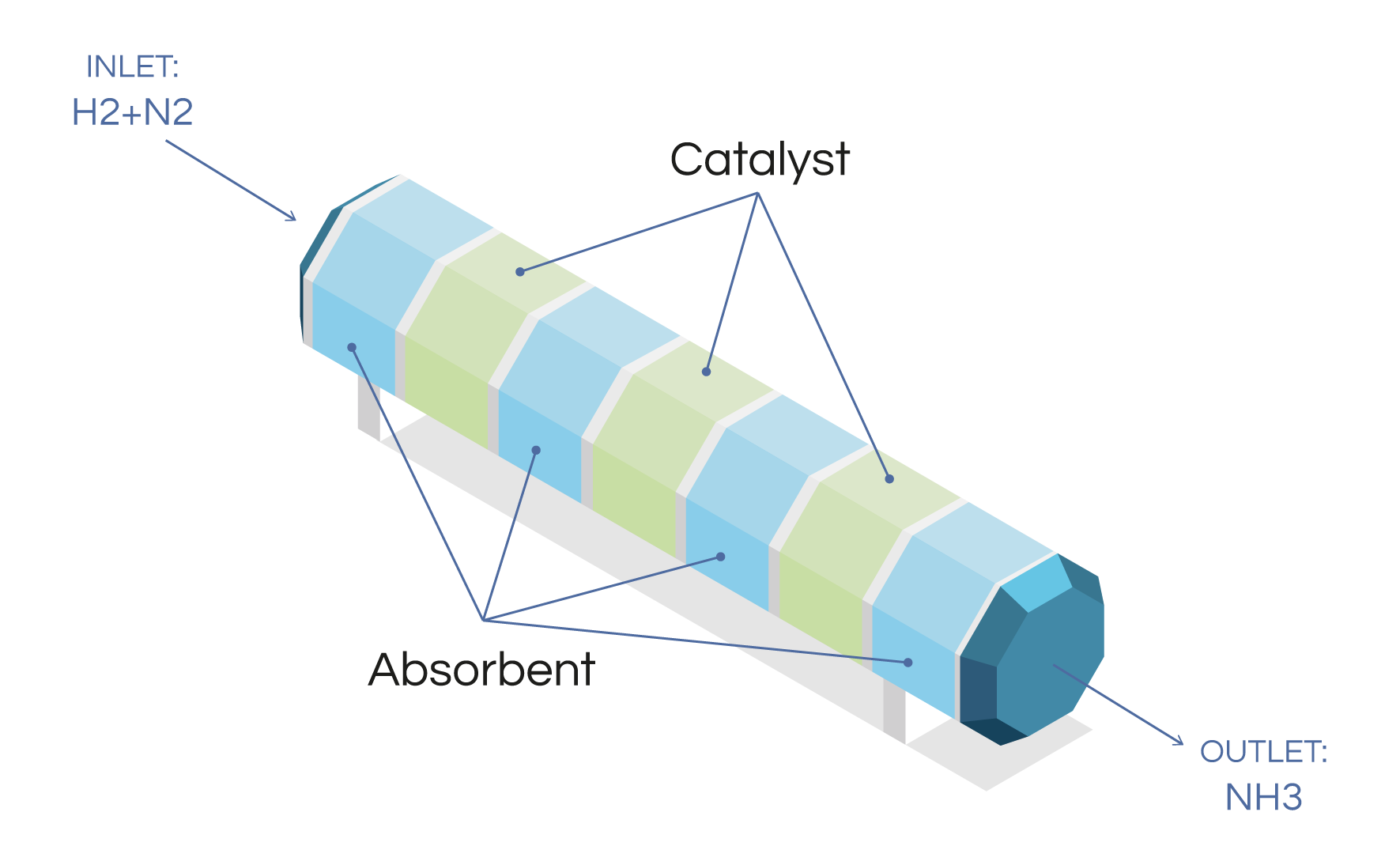
Don’t know the HySTrAm project’s goal yet? The project aims to test the newly developed materials in a TRL5 pilot plant which enables this alternative process for the ammonia synthesis at low pressure and temperature, when compared with the conventional Haber-Bosh process. Its vision is to facilitate a cost-effective production of ammonia, in particular, at low scale in a decentralised manner.
The HySTrAm project has based this process on a breakthrough development of the different key materials. Let’s discover more.
Hydrogen storage
In the current scenario, the vision for hydrogen production revolves around green energy sources. Considering the volatility of these sources, the initial step of the process is to acquire a hydrogen buffer that permits us to store hydrogen during high production moments and release it during low production phases. This would ensure the continuous operation of the synthesis section, even during periods of low energy availability. In this context, the subunit is based on 1) light weight composite vessel and 2) Metal-Organic Framework (MOF) material loaded into the vessel to enhance hydrogen storage through absorption by these materials.
Ammonia synthesis and absorption
The HySTrAm project process is designed to operate at significantly lower pressure and temperature (i.e., 30bar, 300°C) compared to conventional Haber-Bosch processes, resulting in a more cost-effective approach. To achieve it, the project plans to implement the following operational mode:
- Each reactor will operate in a batch mode, with multiple alternating layers of synthesis catalysts and absorbents.
- Syngas will be fed into the reactor where it will be partially synthesized to ammonia in the first catalyst layer and then absorbed in the first absorption layer. After that, the gas will be free of ammonia for further synthesis in the next catalyst layer and so forth.
- The process is intended to be a single pass process with a total absorption per pass of >90%. It is expected that the unconverted gas will be vented.
Subsequently, once the ammonia-absorbing layers reach saturation, the reactor will switch to a desorption mode in which the ammonia will be released by pressure swing and/or by thermal swing. Then, the production will be switched to the next reactor.
Based on the final use and purity requirements, the ammonia released during the desorption stage can either be used directly in the gaseous phase or liquified by condensation – if needed for purity or transportation purposes.
In this framework, the transition from conceptualizing a new process to making it a reality entails a substantial journey, and that’s precisely what AAU Energy and Casale encompassed. But where does this journey stand now?
At this stage, the scientist’s vision takes shape in the form of a Process Flow diagram, which offers an initial visualization of the core process elements, including “what comes in/what goes out”, what are the main subunits (e.g., gas storage, synthesis, produce purification stage, etc.)”, and “what are the main pieces of equipment or blocks (e.g., synthesis reactors, pressure vessel, tanks)”.
The provided information, in its current form, is long way from providing the necessary details to procure the components needed for constructing the pilot plant. Nevertheless, AAU Energy and Casale are consolidating these inputs along with the other findings centered on material development, to create a comprehensive documentation package. This documentation will serve as a basis for acquiring individual components and effectively assembling them into a fully operational pilot plan. To accomplish this, the engineers involved in this endeavour must address the following questions:
- How much gas is flowing where?
- How can we control it?
- Where do we have to know temperature / pressure / composition etc. to be able to control the process?
- How much energy do we have to provide or remove and where?
- How do we provide / remove the energy?
- Is the process safe? What additional instrumentation do we have to add so that the process can be safely run?
- Is the process capable of putting itself automatically in a safe condition in case of emergency? In order to do this, which measurements do we have to have available in the control system and which elements such as shut off valves do we have to have in place in order to achieve that?
- More broadly: based on the initial vision of the process which elements (such as valves etc.) do we need to have in place so that the envisioned control philosophy can be turned into reality?
- What is available from the host site / what are the requirements of the host site in terms of safety / disposal etc.?
- Which data do we need to collect from the pilot so that we can measure that the process is working as expected? Which data is required by the previous WP from the pilot to validate their models?
All responses to the previous questions will be transformed into a comprehensive set of engineering documents that will serve as the definitive guide for every individual component within the pilot plant. Additionally, it will offer detailed information to allow sourcing from the market or in-house manufacturing by the skid manufacturer.
The reactor, as a crucial component of the system, has been designed to facilitate efficient ammonia production thanks to the lower pressure and temperature compared to the conventional Haber-Bosch. The approach integrates both the catalyst and absorbent beds within the reactor, providing a streamlined and compact solution which in principle eliminates the use or the reactant recycling loop. This recycling process adds complexity, cost, and energy consumption to the overall system.
AAU Energy have found out that “due to low temperature and pressure of operation, several beds are necessary to achieve the 90% conversion in a single pass”. But why is this the case? The answer lies in the limited catalyst activity at low temperatures and pressures. Additionally, they have addressed further complications related to the desorption of the synthetized ammonia during the “regeneration” process. During this phase, the reactor will release the ammonia produced during the operation phase. According to Vincenzo Liso, Coordinator of the HysTrAm project and Associate Professor at AAU Energy, “effectively managing this process while ensuring the smooth operation of the other reactor is an area of critical focus”.
It is worth noting that upon successful competition, this will represent a groundbreaking milestone as the world’s inaugural plant of its kind. This HySTrAM project is poised to not only advance our understanding of low-temperature, low-pressure catalytic processes which had been previously proven only at lab scale, but also to make a profound impact on the field providing new possibilities in sustainable ammonia production.